射出成形の概要と選択前に理解しておきたいメリット・デメリット
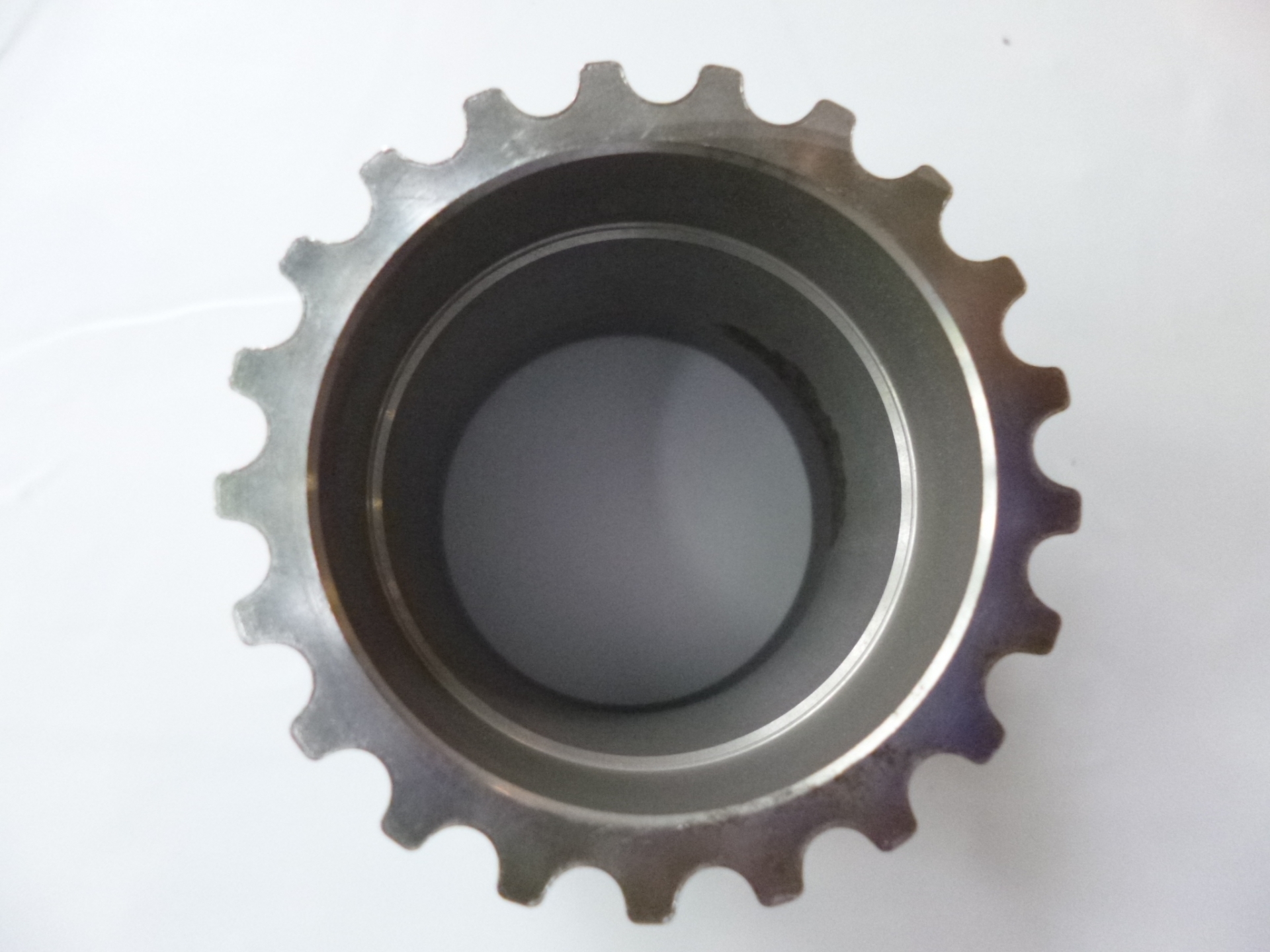
射出成形は、最も一般的なプラスチック成形の方法といわれています。さまざまな製品の製造に適しているため、検討している方が多いでしょう。ただし、すべての用途に対応できるわけではありません。したがって、射出成形を選択する前に、特徴を理解しておくことが必要です。なんとなく選んでいると、具体的な検討段階に入ったときに成形方法の見直しを迫られることがあります。
この記事では、射出成形の概要を解説するとともに、メリット・デメリット、種類なども紹介していきます。以下の内容を参考にすれば、射出成形の概要を理解して、適切に活用できるようになるはずです。プラスチック成形を検討している方は、参考にしてください。
目次
射出成形とは?
射出成形は、プラスチックの成形方法のひとつです。押出成形・ブロー成形と並び、最も一般的なプラスチックの成形方法といえるでしょう。押出成形・ブロー成形が適さない製品は、射出成形で作られることが多くなります。具体的には、バケツやドライバーの取っ手、オフィス機器の歯車、自動車のバンパーなど、幅広いプラスチック製品を挙げることができます。射出成形は、どのようなプラスチックの成形方法なのでしょうか。
プラスチック成形の基本
プラスチック成形の考え方は、成形方法を問わずある程度共通しています。多少の違いはあるものの、基本的には溶けたプラスチックを金型へ流し込んで、冷やし固めてから製品を取り出します。射出成形の場合、200度前後でプラスチック樹脂を溶かして金型へと流し込み冷やし固めます。
射出成形機の構造
射出成形は、英語で「injection molding」と呼ばれるプラスチックの成形方法です。「injection」は日本語で「注射」や「注入」、「molding」は日本語で「成形」を意味します。このことからわかる通り、射出成形機は注射器とよく似た構造をしています。具体的には、駆動装置・ホッパー・スクリュー・シリンダー・ヒーター・ノズル・金型などで構成されます。射出成形機は、油圧モータを組み込んだ油圧式とサーボモータを組み込んだ電動式、油圧モータとサーボモータを組み込んだハイブリット式などに分かれます。また、近年になって、精緻なコントロールを行える射出成形機も登場しています。一昔前に比べると、精度の高い製品を高速で作れる環境が整っているといえるでしょう。
射出成形の成形フロー
射出成形は、どのような流れで進むのでしょうか。続いて、成形フローを紹介していきます。
【射出成形のフロー】
- ホッパーに粒状のプラスチック(プラスチックのペレット)を投入します。
- 粒状のプラスチックがシリンダ内へ送られます。
- 粒状のプラスチックがヒーターで加熱されて溶かされます。
- シリンダ内でスクリューが回転して、溶かされたプラスチックが混練されます。
- スクリューが金型側へ前進し、溶かされたプラスチックが金型のキャビティ(製品と同じ形状の隙間)に射出されます。
- 溶けたプラスチックが金型内で固まるまで圧力を保ちます。
- プラスチックが固まったら金型を開きます。
- 金型のエジェクタピンで製品を押し出し取り出します。
- 金型を閉じて、同じ工程を繰り返します。
上記の工程で注意したいポイントは次のとおりです。
準備
準備段階で型締めの圧力を確認します。型締めは、射出成形機に取り付けられた金型が閉まることを意味します。この点を確認する理由は、圧力が弱いとバリが発生するなど、製品の形が崩れてしまうことがあるからです。ホッパーに粒状のプラスチックを投入する前に、型締めの圧力が正しく設定されていることを確かめます。
スクリューで混練
ホッパーに投入したプラスチックのペレットは、シリンダ内でヒーターに加熱されて液状になります。この工程(材料を液状にする工程)を可塑化と呼びます。可塑化のポイントは、スクリューで液状化したプラスチックを混ぜ合わせて温度を均一にすることです。これにより、金型に射出する材料の量を調整しやすくなります。
射出
プラスチックが液状化したら、シリンダの先端部(ノズル)と金型を接合するノズル接を行います。この状態で液状化したプラスチックを射出して圧力を加えつつ製品を作ります。ポイントは、液状化したプラスチックが逆流しないように適切な圧力を加え続けること、液状化したプラスチックをキャビティ全体に均一に流し込むことなどです。射出成形は連続して製品を製造するため、基本的にノズル接を保ったまま作業を進めます。
冷却と取り出し
金型内に流し込んだプラスチックを冷却させます。冷却のポイントは、金型内で水や油を循環させて、プラスチックに適した温度を保つことです。プラスチックが固まったら、金型を開きエジェクタピンなどを使って製品を取り出します。
射出成形のメリット・デメリット
射出成形は幅広く活用されているプラスチックの成形方法です。幅広く活用されている理由は、メリットが大きいからといえるでしょう。しかし、デメリットがないわけではありません。ここでは、射出成形のメリットとデメリットを紹介します。
メリット
メリットとして次の点が挙げられます。
生産性が高い
最も大きなメリットは、生産性が高いことです。具体的な所要時間はケースで異なりますが、製品によっては1サイクルを数秒で完了させられます。また、1つの金型に複数のキャビティを設けることも可能です。このような金型を利用すれば、1回の射出で複数の製品を作れます。
大量生産で製品単価を抑えられる
大量生産で、製品単価を抑えられる点も魅力です。金型製作後は、材料代しかかかりません。したがって、生産量が増えると製品単価は下がります。そのため、大量生産に向いているプラスチックの成形方法といえるでしょう。
仕上げ加工の手間がかかりにくい
精密に成形できるため他のプラスチックの成形方法よりも仕上げ加工の手間がかかりません。具体的には、ゲートなどの切り離しとバリ取りが必要になる程度です。余計な手間がかからないため、素早く製品を完成させること、コストを抑えつつ製品を完成させることができます。
さまざまな形状の製品を作れる
射出成形は、単純な形状の製品だけでなく複雑な形状の製品も作れます。また、小さな製品から大きな製品まで対応できます。具体的には、直径1mm未満の歯車や全長2mのバンパーなどを製造することが可能です。対応できる製品の幅が広い点も強みといえるでしょう。
デメリット
デメリットとして以下の点が挙げられます。
金型製作に時間がかかる
射出成形では、製造したい製品に合わせて金型を作らなければいけません。所要時間はケースで異なりますが、数カ月程度かかることもあります。生産性の高さは魅力ですが、生産開始まで時間がかかる点には注意が必要です。
金型製作にコストがかかる
金型製作には、ある程度のコストがかかります。したがって、少量多品種生産にはあまり向いていません。金型製作にある程度のコストがかかるため、少量生産だと製品単価が高くなってしまうからです。
あらゆる製品を自由に作れるわけではない
幅広い製品に対応できる射出成形ですが、あらゆる製品を自由に作れるわけではありません。一定以上、一定以下の大きさ、肉厚の製品は作れないことや不良率が高くなることがあります。また、金型から取り出せる形状にする、金型から取りやすくするため1~2%程度の抜き勾配を設けるなども必要です。他のプラスチックの成形方法よりも自由度は高いですが、完全に自由というわけではありません。
一般的な射出成型の種類
射出成形にはさまざまな種類があります。ここでは、一般的な種類を取り上げてみていきましょう。
低圧成形
金型内部に低圧力をかける射出成形です。高圧力をかけるものよりも、バリやガス焼けが起こりにくくなります。修正の手間を省けるため、低コストで製品を作れる可能性があります。また、大型の射出成形機を必要としない点も、コスト面に良い影響を与えます。ただし、圧力のコントロールや射出速度の調整などが難しい点には注意が必要です。オーバーモールディング(ある材料を別の材料上で成形)が必要な電子機器部品などで用いられています。
射出圧縮成形
射出成形に圧縮成形をかけ合わせた方法です。溶けた樹脂を注入してから型締めを行い、金型を完全に閉じる点が特徴といえるでしょう。内部の圧力を一定に保ち、低い圧力で成形を行えます。射出圧縮成形は歪が生じにくいため、光学レンズなどの成形に用いられています。
ガスアシスト射出成形
加熱して溶かした樹脂を金型内部に射出して不活性化ガスを注入する射出成形です。製品内部に中空部を形成できます。また、一般的な射出成形で問題になりがちなソリ・ヒケが生じにくく精度の高い成形を行えます。少量の材料で成形できるため、製造コストを押さえやすい点も魅力です。一般的に、大量生産に向いていると考えられています。ガスアシスト射出成形は、医療機器、産業機器の外装パーツなどに用いられています。
インモールド成形
デザインが印刷されたフィルムを金型に挟み込み射出する方法です。射出時の熱と圧力で、フィルムに印刷されたデザインを製品表面へ転写できます。成形と表面加飾を同時に行える点が特徴です。インモールド成形は、航空機・自動車の内装・外装、アミューズメント機器などに用いられています。
反応射出成形
複数の低分子・低濃度の樹脂を1つの金型内へ射出する方法です。金型内で化学反応を起こすことで固化させます。特徴は、射出の圧力が低いため樹脂製の金型を使用できることです。したがって、金型の製造コストを抑えられます。大型製品にも対応できるため、自動車のウレタン製バンパーなどに活用されています。
特殊な射出成形の種類
続いて、特殊な射出成形の種類を紹介します。
二色成形
2色成形は、2つの樹脂などを組み合わせて1つの製品を製造する射出成形です。具体的には、2つの金型と2つの射出ユニットを用いて、1つのサイクルで2つの射出ユニットから交互に樹脂を射出し、2つの樹脂が組み合わさった1つの製品を製造します。1つの金型内で2つの樹脂を組み合わせた製品が完成するため、組み立ての手間を省ける点が魅力です。2つの部品を別々に作って組み立てるより、工期や人件費を抑えられる可能性があります。2色成形は、医療機器や歯ブラシの製造などに用いられています。
金属射出成形
金属粉末につなぎを加えて射出する方法です。金属粉末を溶解させずに用いる点が、金属塊を溶解させて用いるダイカストなどと異なります。精度・強度とも高い製品を量産できる点が特徴です。金属射出成形(金属粉末射出成形(MIM))は、精密機器・通信機器・医療機器などに活用されています。
インサート成形
金型を締める前にインサート部品を装着して、インサート部品と樹脂が一体化した製品を製造する射出成形です。インサート部品の装着は、人または専用挿入機、ロボットが行います。組立工数を減らせる点、製品の強度を高められる点などが魅力です。インサート成形は、自動車や精密機器の部品などに用いられています。
フィルムインサート、フィルムインモールド成形
フィルムインサート成形は、デザインを印刷したフィルム(シート)を金型に挟み込み樹脂と一緒に成形することで、フィルムと樹脂が一体化した製品を製造する方法です。高度なデザインが可能、キズや汚れに強いなどの特徴があります。家電や自動車、アミューズメント機器などに活用されています。
異材成形
異なる材料を成形工程で組み合わせて、1つの製品を作る射出成形です。各素材の特徴を併せもつ1つの製品を作ることができます。また、組立工数を省けるため、製造コストを抑えられます。異材成形は、歯ブラシ・文房具・おもちゃなどに用いられています。
プラスチックに発泡剤を混ぜ込んで射出成形を行う方法です。
成形時に減圧後微細な気泡が発生しその分の樹脂が節約出来ます。又、発泡力でより均一に収縮するため反りなどが低減できます。自動車、事務機器、容器等に活用されています。
射出成形の特徴を押さえる
この記事では、射出成形の概要やメリット・デメリット、種類などを紹介しました。幅広く用いられているプラスチック成形の方法ですが、全ての用途に適しているわけではありません。特徴を押さえて活用することが重要です。
ジェムス・エンヂニアリングではMoldex3Dを活用した射出発泡ソリューションを提供しております。
ご要望の方は是非当社までご相談ください。