射出発泡成形特集
射出発泡成形の種類
物理発泡材は、主に窒素ガス、炭酸ガスを使用します。相変化によりガスを発生させます。
化学発泡剤には、有機系(ADCA,DPT,OBSH:主にN2ガスを発生)と無機系(炭酸水素塩等:主にCO2を発生)熱分解でガスを生成します。
各々のメリットとデメリットは、下記の通り。
物理発泡 メリット:発泡が良好、発泡倍率大、環境負荷が少ない。
デメリット:初期設備投資が大きい、成形条件幅が狭い。
化学発泡 メリット:発泡が良好、初期設備投資が小さい。
デメリット:発泡倍率小、発泡の制御がより困難。
成形方法種類
主にショートショット法とコアバック法があります。〇ショートショット法とは、金型の中に樹脂を充填させるときに製品部よりも少なく樹脂を充填させて発泡剤の力で、100%の形に作り上げます。
〇コアバック法とは、樹脂を金型に充填させた後に金型の稼働側(発泡させたい箇所)を作動させてその動作の分だけ肉厚を変更しその時の減圧効果で発泡させる。
製品によって、可能、不可と出てくるので肉厚等検討が必須となります。
ショートショット法による軽量化は10~15%前後、コアバック法による軽量化は、30~50%以上が可能となります。
射出発泡成形 MuCell®事例(物理発泡)
物理発泡の一種である微細発泡射出成形は、MuCell®という商標名で知られています。(トレクセル社)
微細発泡を利用することで、軽量化のみならず、ヒケや反りを抑えた射出成形品を安定して生産することが可能になります。自動車の機能・内装部品、電子部品、家電製品、食品容器、医療、消費財、その他一般工業用途などさまざまな分野で幅広く利用されています。MuCell®プロセスは、まず超臨界状態の窒素、または二酸化炭素を溶融ポリマーと混合し、単一相溶解物を形成します。この単一相溶解物を金型内へ射出し発泡させることで、ヒケ、反りが少なく、平面度、真円度等に優れた製品を作り出します。これは、MuCell®プロセスでは従来の充填保圧工程が発泡に置き換えられるため、内部応力の差が少なくなり成形品の収縮が一様となるためです。
こうしたことから、設計形状を忠実に反映できるため成形トライや金型修正の回数を削減でき、コスト面だけでなく開発のスピードアップも可能になります。
こうしたことから、設計形状を忠実に反映できるため成形トライや金型修正の回数を削減でき、コスト面だけでなく開発のスピードアップも可能になります。
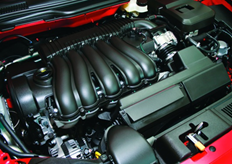
応用が広まる自動車部品
プロセス概要
- 超臨界流体(SCF)の注入
- 2相混在状態
- 拡散進行
- SCF溶解により単一相溶解物を形成
- 急減圧を経て微細発泡構造を形成
必要な設備
- 超臨界流体供給装置
- 超臨界流体インターフェースキットとインジェクター
- 専用スクリューとシリンダー
- シャットオフノズル
射出発泡成形のメリット
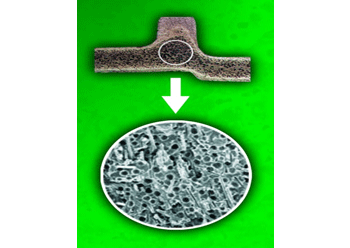
- コスト削減:樹脂消費量の削減(軽量化)、成形サイクルタイムの短縮、成形機型締め力低減、成形機サイズダウン
- 設計自由度:1:1のリブ厚構造、流動性よりも機械特性を重視した材料選定、低反り、寸法安定性の向上
- 開発期間の短縮:金型修正回数、開発期間の削減
薄肉での微細発泡の実現事例(食品容器)
厚みt=0.4mm 軽量化6%
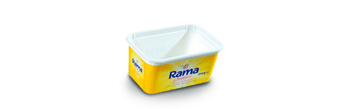
2500トン→1200トンへ変更 サイクル時間15%削減
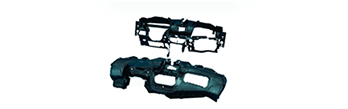
JMS射出発泡トータルソリューション
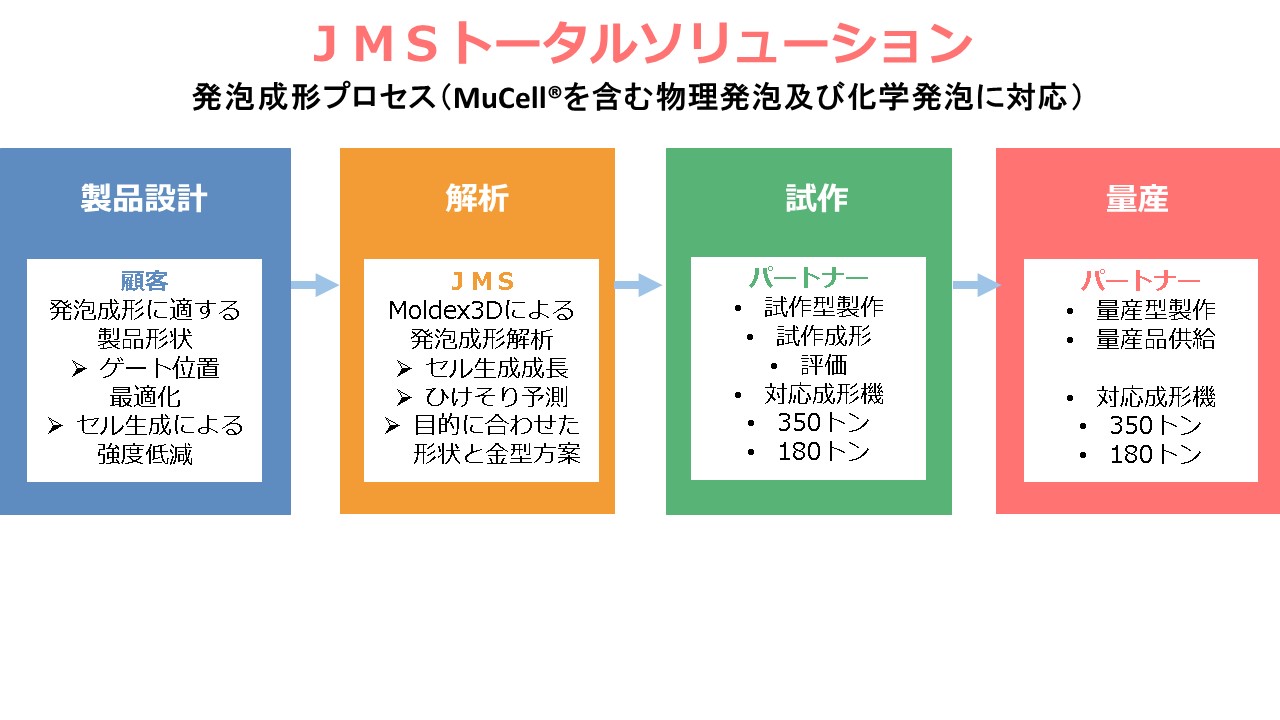
Moldex3Dを利用した射出発泡ソリューション
Moldex3D 射出発泡解析では、発泡核形成と成長に関する動力学を採用して、複雑なプロセスをモデル化しています。。射出発泡成形プロセスを可視化し、複雑な充填挙動や発泡過程に関する深い考察を得ることが出来ます。Moldex3Dは、射出発泡成形による挙動を解明し、事前に影響を予測する事で後戻り工程を削減し、トータルコストの削減につながります。
Moldex3Dは複雑な問題を解決します。
課題 | 1.軽量化が進まない 2.ショートショットになる 3.そりが解決しない 4.表面の品質が課題 通常の射出成形と異なるのは、発泡剤による気泡(セル)の生成です。この生成と成長、そして、その影響を理解し課題を解決する必要があります。 |
---|---|
解析内容 | 通常の結果に加え気泡(セル)サイズや数分布予測を提供します。又、射出成形発泡成形の充填パターンやウェルドラインや重量減を予測します。セル核生成の生成については、独自理論により計算されます。セル分布の影響による収縮とそりの変化も提供します。 解析による分析結果を元に製品の肉厚、ゲート位置及び点数、成形条件の最適化を行います。 |
解析を活用した射出発泡成形工程の理解
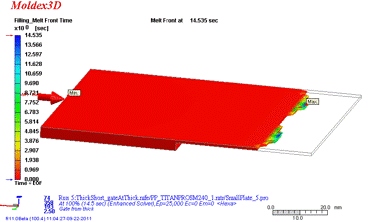
通常のゲート位置で発泡成形の試作を実施した場合に良くある話が、ショートショットの問題である。発泡成形で軽量化をしたいのに、ショートが起こるので樹脂を詰めないといけなくなり、軽量化が出来ない事が起こります。

発泡用のゲート位置で、成形を実施するとショートショットの問題が解決され、又、発泡成形の目的の一つである軽量化を実現する事ができます。発泡成形においてゲート位置は、通常の射出成形より重要になります。
発泡成形を有効に活用するには、発泡がスムーズに行われるようゲート位置等設定する必要があります。
CAEを活用してゲート位置等の最適化を支援しております。
ご要望の際は、こちらの問い合わせフォームよりご相談ください。
次の段付平板モデル(薄肉・厚肉ゲートモデル)について
一般形成および射出発泡成形による流動解析の結果比較。
Moldex3Dを利用した射出発泡ソリューション
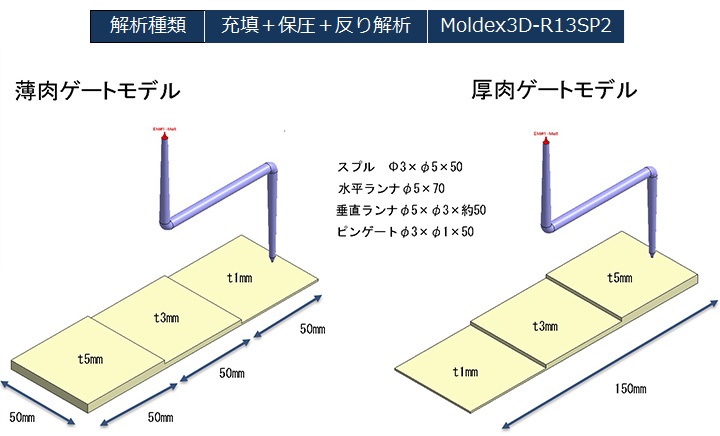
一般成形と射出発泡成形との挙動相違
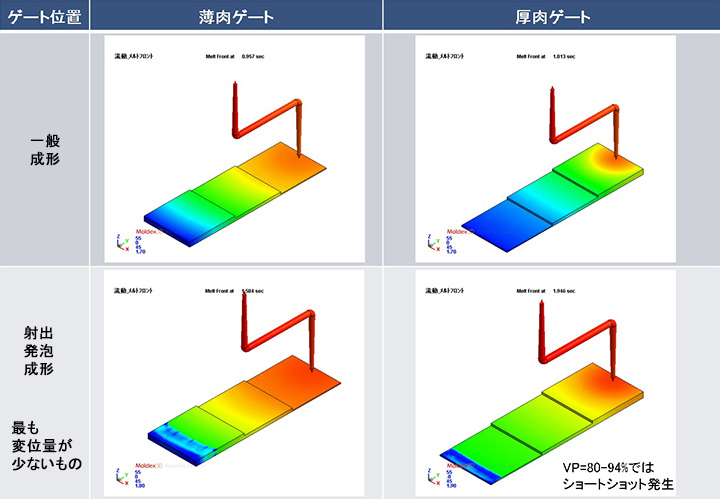
セルサイズ
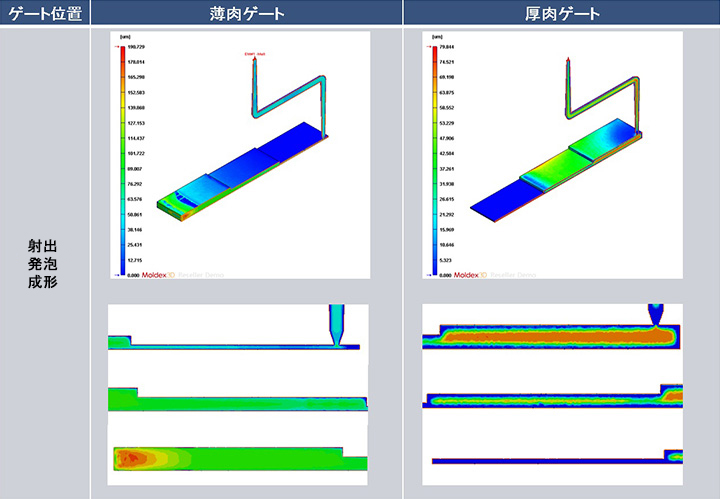
セル密度
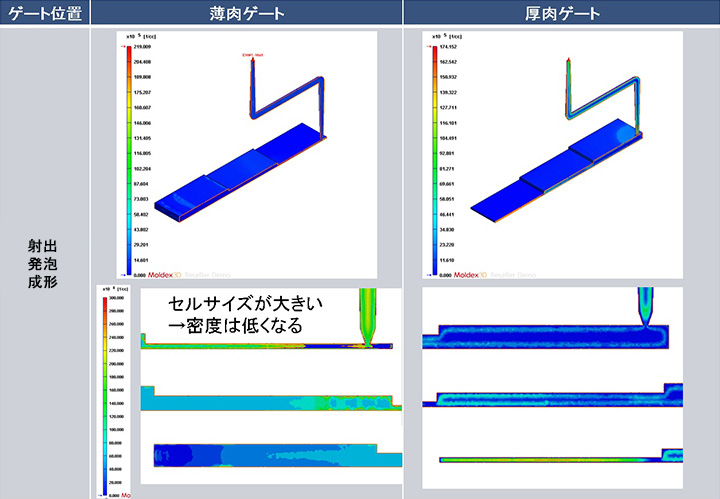
反り解析 X・Y軸

反り解析 Z軸
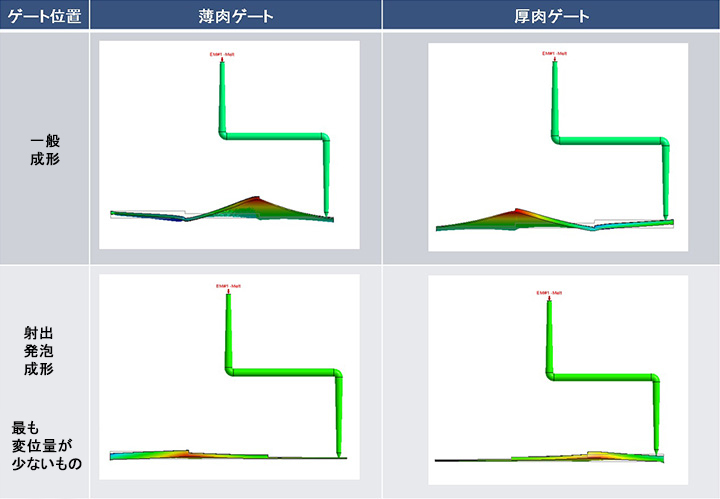