モールドベースとは?構造や構築部品について
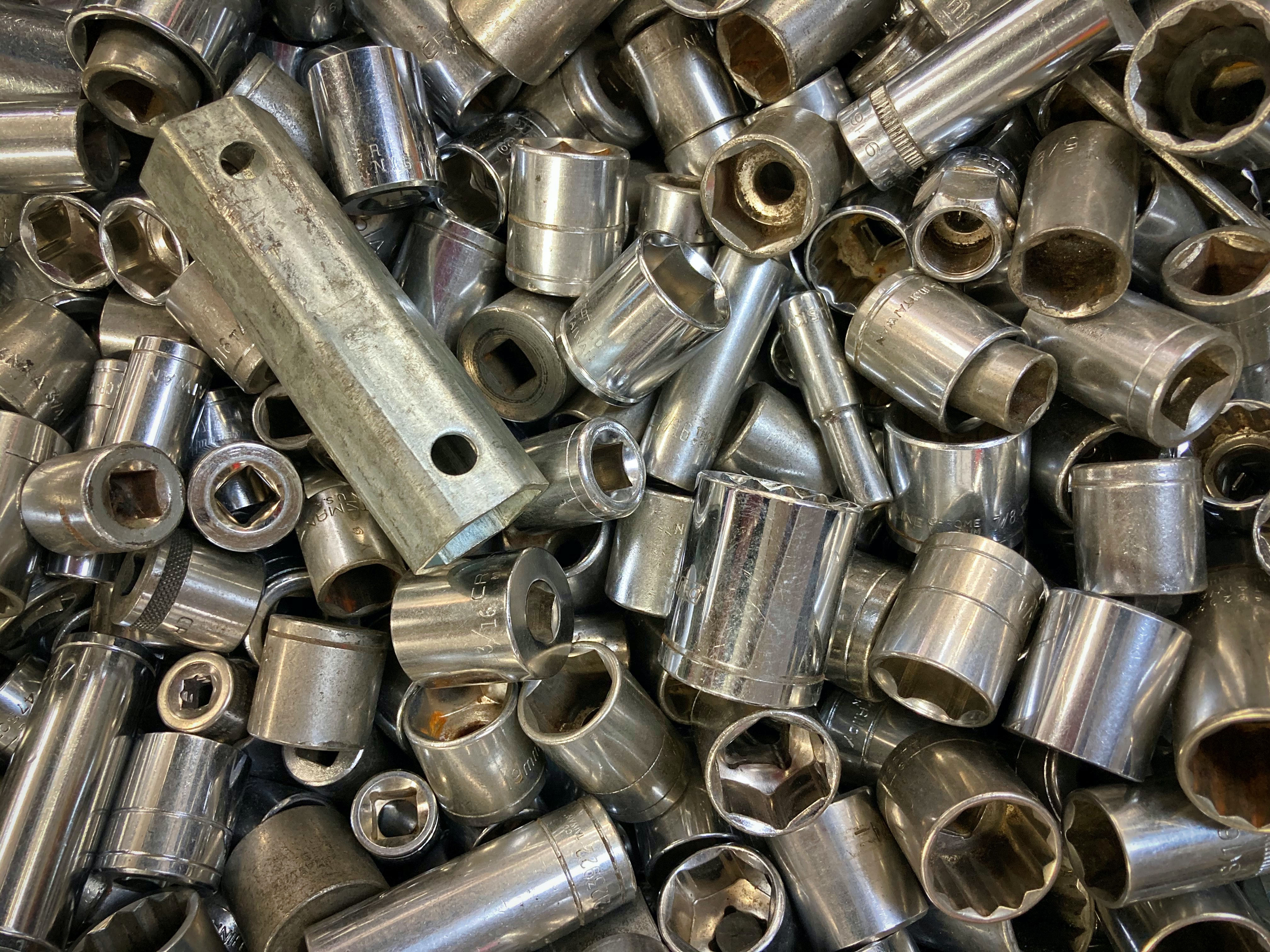
家電製品や私達の生活で多く使われているプラスチックを使った多くの製品を製造するために使われるのが、モールドベースです。
今回はモールドベースについて、構造や構築部品を紹介します。モールドベースをもっと知りたい方や金型の設計や加工に関わる方は必見です。
モールドベースについて
プラスチックの一般的な成形法を行う際に使われる金型部品の総称の名前です。また、金型をプラスチック製品を作るための射出成形機に取り付ける役割もあります。
金型は主に固定側と可動側でできており、2枚の金型の空いた隙間に樹脂を流し込んで固めることで、私達のよく知るプラスチック製品が完成します。樹脂を流し込む隙間の形をいろいろ変えることによって、さまざまな形のプラスチック製品の成形が可能です。
今までは、作るプラスチック製品に合わせて1からモールドベースを設計して、製造していました。現在では、標準規格品が世界的に普及したため、低コスト・短納期につなげられるようになりました。
ただ、とくに大きいものやとくに小さいものなど、特殊な形に関しては現在も製品に合わせて独自に制作するようです。
モールドベースの構造2種類
モールドベースの構造は主に下記の2種類です。
- 2プレート構造
- 3プレート構造
ゲートと呼ばれる場合もあり、それぞれ種類があります。違う部分プレートの枚数や樹脂が金型に流れ込むゲートの形や場所です。
どのプレート構造を使うのかは、金型に樹脂を流し込むときの充填口の形や充填する樹脂の素材で判断します。
以降では、それぞれについて解説します。
2プレート構造
固定側型板・可動側型板とその他以下の4つの部品の計6つで構成されます。
- エジェクタプレート
- ガイドピン
- ガイドプッシュ
- リターンピン
また、2プレート構造には「サイドゲート」と「サブマリンゲート」の2種類があります。両者の違いを見ていきましょう。
サイドゲート
金型のサイド(横)に樹脂が金型に流れ込むゲートがあります。複数の製品を一度に充填できるので、小さく多くの製品を加工する際に使用されます。
デメリットは製品側にゲートのあとである突起が残ってしまう可能性がある点です。突起が残ってしまうので切断する手間があります。
サブマリンゲート
金型を開閉した際に、成形したものとゲートのあとである突起部分を自動で切断してくれるので、わざわざ突起を切断する必要がありません。サイドゲートよりも効率的な生産が可能です。
デメリットは、流れの悪い樹脂を使用する際に、金型内に樹脂が十分に充填できない可能性があります。
3プレート構造
以下の6つの部品とストリッパープレート(3プレート構造のみ)の計7つで構成されます。
- 固定側型板
- 可動側型板
- エジェクタプレート
- ガイドピン
- ガイドプッシュ
- リターンピン
3プレート構造には、「ピンゲート」と呼ばれる種類があるので紹介します。
ピンゲート
多くの製品を一度に作るときに使われます。樹脂を流し込む部分が細く、金型を開いたときにゲートのあとにある突起が自動で切断されます。
デメリットとして、樹脂を流し込む部分が細く小さいので流れの悪い樹脂を使用すると、成形不良になる可能性があるので注意してください。
モールドベースを構築している各部品
ここでは、モールドベースを構築する総称部品9つと、その他の大事な部品3つについてくわしく解説します。
モールドベースの総称部品9つ
以下の9つの部品で完成する金型を「モールドベース」と呼びます。
- 固定側取付板
- 固定側主板
- 可動側主板
- 突出板
- スペーサーブロック
- リターンピン
- 可動側取付板
- ガイドピン
- ガイドブッシュ
モールドベースは、企業が成形するプラスチック製品の規格化に合わせたサイズが市販で売られているので、納期の短期化や低コストが実現できます。
製品の形状や大きさにもよりますが、市販のものが使用できればそちらの方がいいでしょう。以降では、各部品について説明していきます。
1.固定側取付板
固定側型板の取り付けや金型を射出成形機にセットするために必要なプレートです。
2.固定側主板
金型の主体部分であり、成形したものの表面部分を形作ります。
3.可動側主板
固定側主板の対になる金型の主体部分であり、成形したものの内部の形を作ります。
成形部分の凹凸の付け方は型板に直接掘る方法や入れ子構造にする方法があります。入れ子構造にした場合、部品交換や加工がやりやすいです。
4.突出板
主に、上板と下板の2枚で構成され、上板に突き出しピンとリターンピンを取り付け、それを下板で押さえて固定します。突出板を成形機が突き上げたら、成形したものが取り出せます。
5.スペーサーブロック
突出板が成形したものを取り出すため、突き上げる際の空間を確保するためのプレートです。
6.リターンピン
成形したものを取り出すために突き出した突出板を金型が閉じる際、一番最初に固定側型板に当てることで定位置に押し戻します。
また、成形したものを取り出すための突き出しのバランスを保つための役割もあります。
7.可動側取付板
可動側型板・スペーサーブロックの取り付けやプラスチック製品を作るための射出成形機に設置するためのプレートです。
8.ガイドピン
金型を開閉する際に固定側と可動側の位置を合わせるピンです。
9.ガイドブッシュ
ガイドピンをはめ込んで部品同士の隙間を埋める部分です。
その他の大事な部品3つ
重要な部品は先ほど紹介した9つだけではありません。
- ロケートリング
- スプルーブッシュ
- 突き出しピン
上記の3つの部品は総称部品ではありませんが、それぞれ大事な役割が存在します。それぞれについて見ていきましょう。
1.ロケートリング
成形機に金型を真ん中に取り付けるときに使われるリングです。凸状の部分を成形機にある固定盤の穴に合わせることで、金型を成形機の真ん中に取り付けが可能です。
2.スプルーブッシュ
金型に樹脂を充填する部品です。摩擦が激しいので、消耗品として交換ができる部品にされています。
3.突き出しピン
金型から成形したものを押し出すためのピンです。ただし、押し出すのは突き出しピン以外が使われるケースもあります。
モールドベースの素材
部品の多くは、炭素やクロムを添付した工具用の鋼である機械構成用炭素鋼(S55Cなど)が素材として使用されています。この素材の優れている部分は下記の4つです。
- 強度
- 弾性
- 靭性
- 熱伝導の高さ
上記以外に錆びにくくして欲しい、耐久性を上げたいといったときには、以下の特殊な3つの素材を使う場合もあります。
- プリハードン鋼
- ステンレス鋼
- アルミニウム合金
すべての部品に特殊な3つの素材を使う場合もありますが、入れ子構造を使用するときは入れ子部分だけに特殊な素材を使う場合が多いです。
モールドベースの構造や構築部品について
今回はモールドベースとは何か、構造、構築部品について紹介しました。
私達の生活の中でプラスチック製品は多く使われていますが、そのプラスチック製品を作るために欠かせないのがモールドベースです。
モールドべースにはどのような種類があり、どんな部品で構築されているかわかってもらえましたか?
作るプラスチック製品の大きさや量、用途、樹脂に合わせて使用するモールドベースを使い分けるようにしましょう。
もし、モールドベースについて興味があればぜひ一度ご相談ください。
ジェムス・エンヂニアリングでは特注モールドベースの加工や各プレート類の製作を行っております。ぜひ当社のHPをご覧ください。