放電加工のメリット・デメリットについて
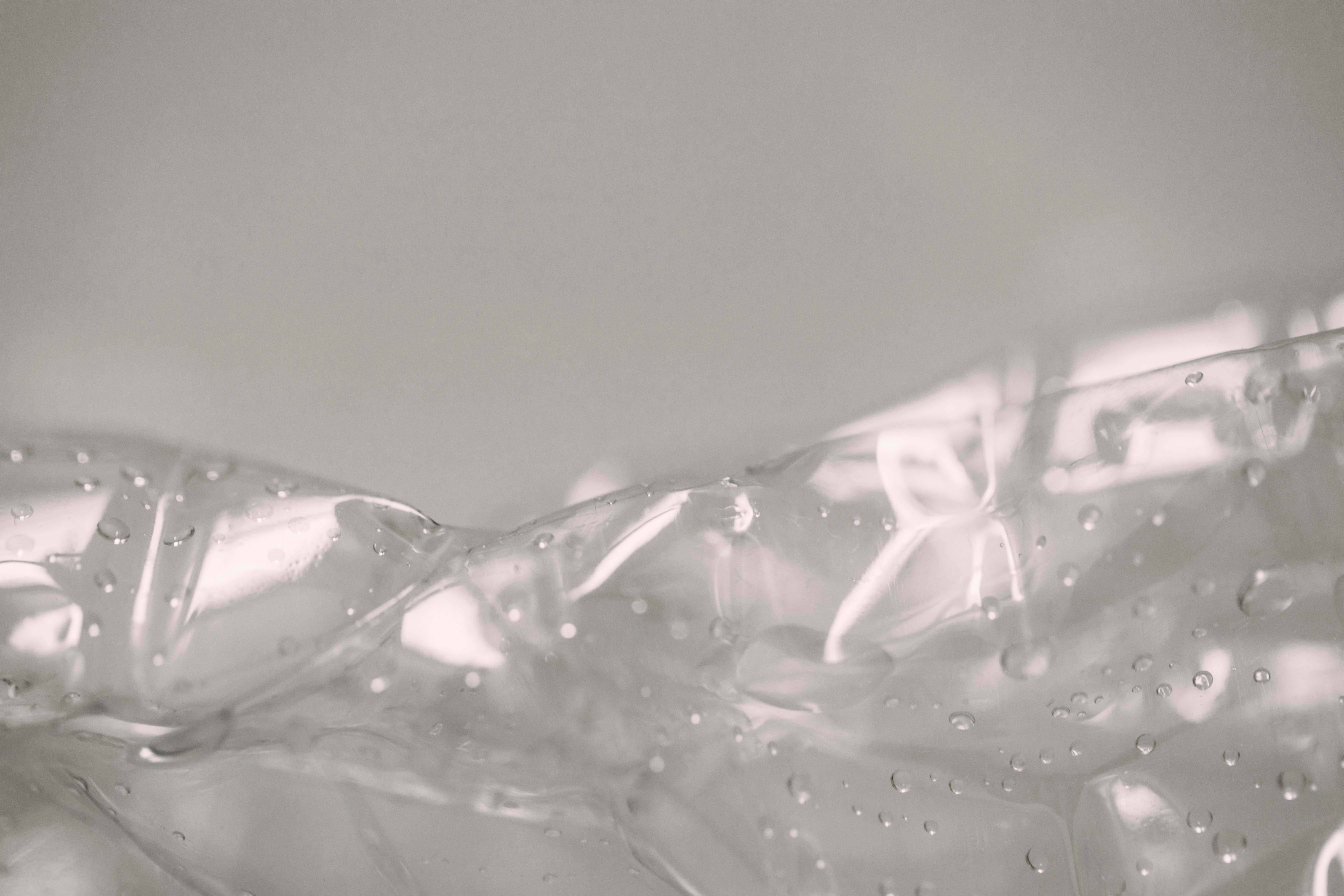
金属を切断や加工する方法としてよく用いられる放電加工。
今回は、そんな放電加工のメリット・デメリットや使われている素材、似た加工方法についてなどくわしく紹介していきます。放電加工とはどんなものかより深い知識をつけたい方必見です。
放電加工とは
放電加工とは、電気の力(熱)を使って金属を溶かし切断や加工を行う方法です。水や油などの液体の中で加工対象の金属と放電加工機の間に放電する(電気を流す)と、電気の力(熱)で金属を溶かします。
このとき、溶けた金属は周りの液体で冷やされ、液体内に飛散しており、電気の力を受けた加工対象の金属はクレーターのように凹みます。
- 電気の力で加工対象の金属を溶かす
- 溶かされたものは液体内に飛散
- 電気の力を受けた部分がクレーターのように凹む
これを繰り返し、金属の切断や加工を行います。
放電加工のメリットとデメリット
金属の切断や加工に使われる放電加工ですが、もちろんメリットとデメリットがあります。
放電加工を行う際には必ず、メリットとデメリットの両方を知っておきましょう。
メリット
まず、放電加工のメリットは以下の5つです。
- 高度な加工ができる
- 素材によって切断方法を変えなくてもいい
- 対象物に対して負荷が少ない
- 熱による変形がほぼない
- 機械が壊れにくい
それではそれぞれくわしく見ていきましょう。
高度な加工ができる
切断や加工と言えば工具を使い、削ったり切断したりする切削加工を思い浮かべるかもしれません。しかし、放電加工は切削加工に比べて細かい形状でも1ミクロンの細かさで加工できるくらいに高精度での加工が可能です。
1ミクロンまでの細かさの加工となると切削加工ではかなり難しいです。
素材によって切断方法を変えなくてもいい
放電加工の場合、電気の力によって切断や加工を行うため硬い素材でも、問題なく切断、加工が可能です。
もし、刃物などを使った切断や加工を行う場合、切断や加工を行う対象物よりも刃物が硬い必要があります。刃物よりも対象物の方が硬かった場合、刃物が負けてしまい欠けたり折れたりする可能性があります。
そのため、対象物よりも硬い素材の刃物や工具を用意する必要がありますが、放電加工の場合は素材によって切断方法などを変える必要がありません。
対象物に対して負荷が少ない
切断や加工を行う際は、放電加工機と対象物の間に放電を行います。なので、放電加工機が直接対象物に触れないため、応力(物体が外部から力を受けた際に物体の内部から発生する力)が発生しません。
また、残留応力が原因の寸法の誤差が起こる心配もありません。
熱による変形がほぼない
放電加工は電気の熱を使い切断や加工を行うため、熱による変形を心配する方もいますが、熱による変形はほぼありません。
「放電加工とは」でも記載した通り放電加工を行う際、対象物は水や油などの液体の中にある状態です。これらの液体によって常に冷却されているため、熱による変形の心配はほぼありません。
機械が壊れにくい
放電加工を行う機械は壊れにくいと言われています。その理由は「対象物に対して負荷が少ない」でも記載しましたが、対象物と触れずに放電して切断や加工を行うからです。
切断や加工の際に対象物とは触れ合わないため、取り替えなければ行けない部品などはありますが、放電加工の機械は壊れにくいです。
デメリット
放電加工にはかなり魅力的なメリットが多いですが、当然デメリットもあります。
- 時間がかかる
- 加工ができない素材がある
- 消耗に応じて取り替えが必要な部品がある
- 電極を作成しないといけない
- 一部できない加工がある
それではデメリットについてもくわしく紹介していきます。
時間がかかる
どのような加工を行うかにもよりますが、放電加工は時間がかかります。
放電した熱で金属を溶かして加工を行いますが、一度の放電で削れる部分は多くないため、何度も放電し金属を溶かす工程を繰り返します。
そのため、どうしても時間がかかってしまい、短期間で量産するには不向きです。
加工ができない素材がある
放電加工は放電による熱で金属を溶かし、加工するため通電性のない素材では放電しないため熱が発生しないので金属が溶けず、加工できません。
金属の定義として通電性があるといった条件があるため、金属であれば基本的に加工ができると思っていいでしょう。
ただし、金属の中にも通電するものの、他の金属と比べて通電性が低いステンレスなどは加工が難しい場合があります。
消耗に応じて取り替えが必要な部品がある
放電加工では電極を使用しますが、加工時に放電をして熱で金属を溶かすため、加工対象物だけではなく放電加工機側の電極も熱によってわずかに溶けていきます。
とくに、型彫り放電加工の場合、電極の角の部分が熱で溶けてしまうと想像通りの完成にはなりません。消耗具合を見て取り換えが必要です。
電極を作成しないといけない
型彫り放電加工に限ってですが、加工する形に合わせた電極をわざわざ作る必要があります。
加工を始める前にまずは電極を作る工程が入るため、時間がかかる放電加工の中でもより時間がかかり、生産性は下がってしまいます。
一部できない加工がある
ワイヤー放電加工は糸のように張ったワイヤーを使い加工を行います。ワイヤーは垂直方向に張って、そのワイヤーに向けて金属を差し込み加工するため、水平方向に切断するなど一部できない加工があります。
放電加工の素材
放電加工の電極の素材にはさまざまな金属が使われています。
- 電極の消耗
- 形状加工性
- 材料コスト
上記を考慮して主に下記の4つの金属が電極として使用されます。
- 銅
- グラファイト(黒鉛)
- 銅タングステン
- 銀タングステン
では、それぞれの金属の特徴などを紹介していきましょう。
銅
電極に使用する素材としてはコスト面などの理由で最も基本的でよく使われています。とくに、型彫り放電加工の電極としてよく選ばれます。
銅を電極として使用するメリットは主に4つです。
- 低コスト
- 電極の形が豊富にある
- 電気抵抗が低い
- 熱伝導がいい
これらのメリットに対して、銅を電極として使用するデメリットは主に2つあります。
- 機械加工性が低い
- 熱膨張係数が大きい
熱膨張係数が大きいと電気の熱で加工を行う際に電極の寸法が熱膨張で変わってしまうため、細かく繊細な加工では避けた方がいいでしょう。
しかし、型彫り放電加工を行う場合、低コストであり電極の形が豊富にあるため、細かく繊細な加工ではない場合は多くの場面で銅が選ばれています。
グラファイト(黒鉛)
グラファイトは黒鉛(こくえん)と呼ばれる場合があり、鉛といった漢字が含まれていますが鉛(Pb)とは別です。ダイヤモンドや石炭と同じ炭素の仲間であり、鉛筆の芯の原料としても使われています。
そんなグラファイトを電極として使う場合のメリットは3つあります。
- 耐熱性が高い
- 機械加工性が良い
- 熱膨張係数が低い(銅の1/3)
これらのメリットに対して、デメリットは2つあります。
- 面粗さが劣る
- 異常放電する場合があり電極消耗を大きくした放電条件にする必要がある
グラファイトはその性質上、通電性や耐熱性に優れているため電極制作の効率が高いです。
耐熱性に優れているため、とくに、硬い材料の加工の際に荒加工を行うために使われる場合が多いです。
銅タングステン
銅タングステンは銅とタングステンを混ぜ合わせた金属です。
タングステンとはスウェーデンの言葉で”重い石”という意味があります。とても重く硬いレアメタルで、金属の中でもとくに超高温の環境にあっても形状安定性(融点)が高いです。
あまり聞き慣れないかもしれませんが、硬さや形状安定性の高さから、工業用や医療用としてさまざまな分野で利用されています。
そんな銅タングステンを電極として使用するメリットは主に4つあります。
- 銅の熱伝導とタングステンの融点といったそれぞれの利点を持っている
- 機械加工性が良い
- 低消耗で加工ができる
- とくに硬い材料の加工ができる
これらのメリットに対してデメリットは主に2つです。
- 高コスト(銅の約40~50倍)
- 銅と比べて加工速度は早いが電極の消耗が激しい
銅タングステンは、銅にあるメリットにタングステンのメリットをかけ合わせているため、多くの加工に使用されています。とくに、型彫り放電加工にて使用される場合が多いです。
銀タングステン
銀タングステンは銀とタングステンを混ぜ合わせた金属です。タングステンの説明については「銅タングステン」に記載しています。
銀タングステンを電極として使用するメリットは主に5つあります。
- 機械加工性が良い
- 放電加工性が良い
- 剛性(物体の体積の変化を伴わない形の変化に対する弾性)が高い
- 繊細な加工に適している
- とくに硬い材料の加工に適している
これらのメリットに対するデメリットは、高コスト(銅の約80~100倍)である点だけです。
銀タングステンは、放電加工を行ううえでかなり良い特性を持っており、消耗の低い加工もできるので加工全般に使用できます。
しかし、コストがかなりかかってしまうため、高精度な加工が必要な場合や高単価な案件でのみ使用される場合が多いです。
放電加工の用途
放電加工では7つの加工ができます。
- 人工欠陥
- 六角穴
- キー溝
- 角出し
- ネジ加工
- 深穴加工
- 斜め穴
それぞれどのような加工か紹介していきます。
人工欠陥
人工欠陥とは、人工的に欠陥を作る加工です。
なぜわざわざ欠陥を作るのかと思うかもしれませんが、企業は金属製品が欠陥によってどの程度強度が下がるのかといった試験を商品化する前に必ず行います。
その際に、欠陥を人工的に作る場合があり、放電加工が使用されています。
六角穴
私達の生活でも家具などを組み立てる際に、六角の穴が空いたネジを使った経験はあるのではないでしょうか?家具などの組み立てに使用される六角ネジは、切削加工などで大量生産されています。
しかし、鉄橋や鉄塔を作る際にはより丈夫で硬い素材の六角ネジが必要です。その際の六角穴を作るときに放電加工が使用されています。
キー溝
キー溝加工とは接続する部品同士が動かないように部品内に加工を行うものです。多くの場合、スロッター加工といった刃を取りつけた機械の上下往復運動によって加工を行います。
しかし、スロッター加工の場合、底つきや大きいものに対するキー溝加工が難しい場合は放電加工で加工を行います。
角出し
切削加工などの場合、複雑な形の角出し加工はかなり難しいとされていましたが放電加工では複雑な角出しでも加工が可能です。
また、回転工具を使った角出しの場合角R(角の丸み)がついてしまいますが、放電加工では角Rがほぼない加工ができます。
ネジ加工
焼入れをしたあとでネジの切り忘れに気づいた場合や、旋盤でネジを切ったあとにもっと深くしたい場合でも放電加工であれば加工できます。
深穴加工
ドリルなどの刃物で深穴加工を行う場合、難易度を表すアスペクト比30以上は加工が困難とされています。
しかし、放電加工の場合はアスペクト比100のかなり難しい深穴加工でも対応できます。
斜め穴
切削加工などの刃物やドリルを使って斜めの角度で穴を開けたい加工をしたい場合、その角度によっては穴を開けたい部分から刃物が逃げてしまう可能性があります。
しかし、放電加工であれば、どれほど角度があっても開けたい部分に穴を開けられます。
放電加工機の特徴
放電加工機の特徴は主に5つあります。
- 高度な加工ができる
- 素材によって切断方法を変えなくてもいい
- 対象物に対して負荷が少ない
- 熱による変形がほぼない
- 機械が壊れにくい
これらの特徴があるため、切削加工などの刃物やドリルを使った場合では難しい、細く繊細な加工やとても硬い素材への加工が可能となっています。
しかし、デメリットももちろんあります。
- 時間がかかる
- 加工ができない素材がある
- 消耗に応じて取り替えが必要な部品がある
- 電極を作成しないといけない
- 一部できない加工がある
これらのメリット・デメリットについては上記の「放電加工のメリットとデメリット」でくわしく触れています。ぜひそちらをご覧ください。
放電加工機の種類
放電加工機にはいくつかの種類があります。
- 型彫り放電加工機
- ワイヤー放電加工機
- 細穴放電加工機
今回は、よく使われる上記の3種類に絞って紹介します。
型彫り放電加工機
型彫り放電加工機は、加工したい形の電極を作りハンコを押すように対象物に近づけ、放電・電極の形をそのまま転写する加工法です。
電極は切削加工などで作られる場合が多いため、電極の素材は銅やグラファイトなどの比較的柔らかい加工しやすい金属が使われます。
加工する形に合わせて電極を作る所から始めるため、コストと時間はかかってしまいますが複雑な形でも細かく高精度な加工ができます。
また、ハンコを押すように電極を近づけて放電させるため、貫通させずに底つきのままの形でも加工が可能です。
ワイヤー放電加工機
ワイヤー放電加工機は細さ0.05〜0.3mmのワイヤーを電極として加工を行います。ワイヤーの素材には黄銅が使われる場合が多いです。
加工したい形によって電極の加工をする必要はありません。糸のこぎりで木材などを切るように対象物を切断、加工を行うので底つきのままの加工はできません。
細穴放電加工機
細穴放電加工機は名前からも分かる通り、細い穴を開けたい場合に使用します。開けたい穴の大きさに合わせた棒状やパイプ状の電極を、対象物に近づけると放電し穴を開けます。
硬い素材や細く深い穴を開けるのは切削加工ではかなり困難とされていましたが、細穴放電加工機では全く問題なく加工が可能です。
放電加工と電解加工の違い
放電加工とかなり似た加工方法として電解加工といった方法がありますが、これらの違いは対象物を溶解させる方法です。
電解加工とは電極と対象物の間に放電を行い、放電を行った状態でアルカリ性の電解液をかけて化学的に対象物を溶解させて加工を行います。どちらも通電性のある素材であれば加工できます。
- 放電加工は放電する熱によって対象物を溶解し加工する
- 電解加工は放電した状態で電解液をかけて化学的に溶解し加工する
上記の部分が放電加工と電解加工の主な違いです。
プラズマ加工について
プラズマ加工とは、放電加工を応用した加工方法です。放電で発生したエネルギーをノズルから噴射(プラズマジェット)して対象物を切断します。
放電加工とは違い、通電性のない素材でも加工ができ、通電性の低い合金やステンレスの厚い板の切断などに使われます。通電性のないものや通電性の低いものの加工方法としてレーザー加工などもあります。
しかし、レーザー加工よりもコストが低く切断面もきれいなためプラズマ加工を選ぶ場合が多いです。プラズマ加工を行う際には、プラズマ加工機を使います。
微細放電加工
微細放電加工とは放電加工の中でもとくに微細加工を行うための加工方法です。
極細放電加工では、極細の電極と微小な放電エネルギーを使用し500μm以下の加工を行います。電子部品や光学部品など極細部品の成形に多く採用されています。
放電加工とは何かを理解しましょう
いかがでしたか?
今回は放電加工のメリットやデメリット、放電加工の素材やできる加工、種類について紹介してきました。
放電加工は通電性のある素材であれば、かなりメリットの多い加工方法です。しかし、メリットが多い加工方法ではあるものの、デメリットがない訳ではありません。
放電加工のメリットやデメリット、できる加工、得意な加工などをしっかりと理解したうえで、加工したい素材や形に合わせた加工方法を選べるようになりましょう。
もし、放電加工を行いたい方や興味がある方は一度当社にご相談ください。
ジェムス・エンヂニアリングでは放電加工を含めた型板の全加工や入れ子の全加工ができます。興味のある方はぜひ当社のHPをご覧ください。