射出成形における成形不良の種類・原因と対策方法
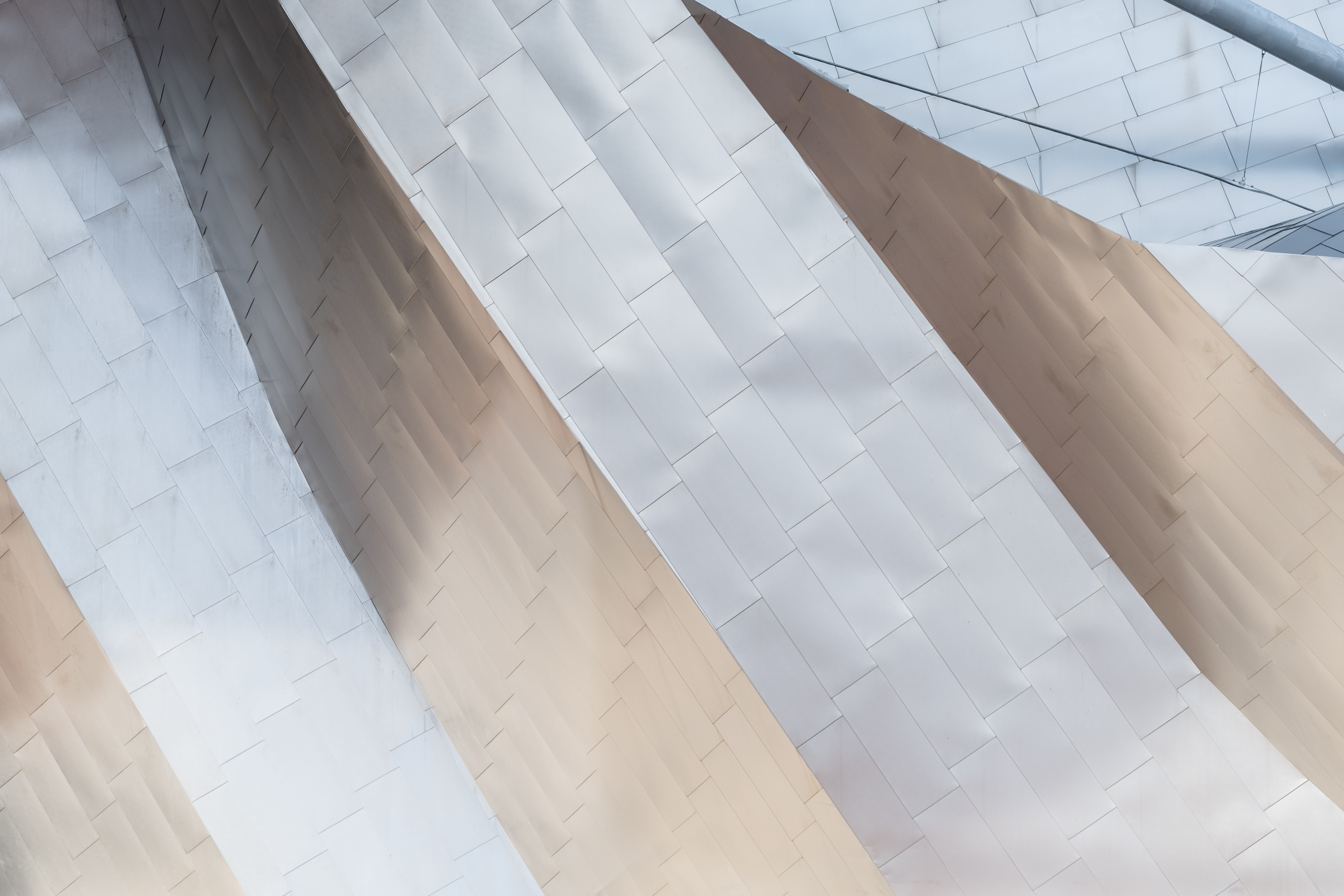
- 射出成形による成形不良と対策方法
- バリの原因と対策
- 反りの原因と対策
- ウェルドラインの原因と対策
- ボイドの原因と対策
- フローマークの原因と対策
- シルバーストリークの原因と対策
- ヒケの原因と対策
- 成形不良品ゼロを目指そう
射出成形とは、主に合成樹脂(プラスチック)を原料にした製品生産の加工法です。
さまざまな形の製品を大量生産でき、導入している企業もたくさんあります。
しかしながら、成形品が設計通りの形状にならなかったり、不良品ができたりと、上手くいかないこともあるかもしれません。
不具合が出てしまうと、場合によっては再処理や処分となることもあり、労働時間や材料費に影響を与えるため、できるだけ避けたいところです。
今回の記事でご紹介するのは、射出成形における成形不良の代表的な種類とその対策について。
成形不良で悩んでいる方や今後成形不良品ゼロを目指したい人は、ぜひ参考にしてみてください。
射出成形による成形不良と対策方法
射出成形の製造現場における課題のひとつに、素材や射出速度、温度など、さまざまな要因により発生する成形不良があります。
成形不良品は商品にならないこともあり、できるだけ成形不良にならないような対策が必要です。
バリの原因と対策
完成した成形品のつなぎ目に付着している薄い樹脂がバリです。
バリがあることによる使用上の違いはありませんが、製品の見た目が低下するため、バリがないに越したことはありません。
バリが発生する理由は、金型に何らかの原因により隙間ができ、そこから樹脂が溢れてしまうことにあります。
金型に隙間ができる原因としては、金型の合わせに隙間がある、金型の強度が弱く樹脂圧で隙間が開く、過度な射出圧力や射出スピードにより合わせ面が開いたりプレートが曲がったりする、といったことが挙げられるでしょう。
金型に隙間がある場合は、修理が必要となります。
高射出圧力・高射出スピードが最近の傾向ですが、金型の強度がそれに対応していない可能性も考えられます。
重要となるのは、金型が開いたり歪んだりすることのない充填圧で成形すること。
バリが発生しやすいなら、低圧成形に変えてみるのも対策のひとつです。
反りの原因と対策
設計上ではまっすぐに仕上がるはずなのに、できた成形品が成形直後、もしくは成形後に反ってしまう現象が、反りです。
反り以外にも、曲がり、ねじれと呼ばれることもあります。
反りが起こると、製品の見た目への影響以外にも、上手く組み立てられなかったり隙間が生じてしまったりと、不具合の原因になることもあるでしょう。
反りの発生は、収縮の不均一が原因です。
収縮が不均一になるのは、温度と圧力のバラつき、金型温度のバラつき、繊維配合による収縮の異方向という理由が挙げられます。
金型内の樹脂は、温度が高ければ高いほど、圧力が低ければ低いほど、収縮が大きくなります。
製品の厚さの差をできるだけ少なくすることで、温度と圧力の差が少なくなり、反りが起こりにくくなるでしょう。
また、樹脂に触れる金型の温度のバラつきにより、収縮差が生じていることもあります。
冷媒温度や冷却管のレイアウトを見直し、金型内の温度差を可能な限り小さくしてみてください。
繊維強化プラスチックの場合、収縮方法の違いにより反りが発生しているケースもあります。
この場合、繊維の方向をランダムにすることで異方向性収縮を抑えるのも、対策のひとつです。
ウェルドラインの原因と対策
成形品の表面に現れるライン状の模様が、ウェルドラインです。
射出成形において、金型内の樹脂が合流する場所に跡が残ったもの。
製品の見た目を損ねたり、傷と間違えられたりする他にも、ウェルドラインの位置に負荷が加わると破損しやすいなど、強度の問題にもなることもあります。
ウェルドラインは、射出成形の工程でどうしても発生してしまう現象のため、なくすことはできません。
見た目に影響を及ぼす箇所や、負荷がかかる箇所など、ウェルドラインを発生させてはいけない範囲を見極め、そこにウェルドラインが出ないよう調整することが大切です。
ウェルドラインができる箇所はゲートの位置に由来し、ゲート位置を変えることで調整することができるでしょう。
ゲート位置を変えられない場合は、バルブゲート開閉のタイミングをズラしてみるといいかもしれません。
ボイドの原因と対策
ボイドとは、成形品の中に泡のような空洞が発生する現象のこと。
製品の強度を低下させる要因になることもある成形不良です。
内部に発生する不良のため、透明でないと分からないこともあり、見落とされることもあります。
このボイドの発生原因は、樹脂の収縮率と温度。
冷却の際、樹脂の表面が固まったあとに内部が冷えるという流れになり、冷えた箇所から順に収縮していきます。
冷却の早い外側に内側の材料が引っ張られ、表面硬度が高い場合には外側でなく内側にボイドが発生します。
ボイドの対策としては、金型の温度を下げる、射出保圧を上げる、保圧時間を長くする、樹脂温を下げるなどして、成形品の外側と内側の冷却速度の差を縮めることが有効です。
フローマークの原因と対策
フローマークとは、射出の際に生じる流れ模様が残ってしまう現象。
ゲートの箇所を中心にしてできることが多いのですが、材料や成形品の形状などによっても発生の仕方が異なります。
見た目にも関わる成形不良のため、品質に関わる製品の場合、不良品となってしまうこともあるでしょう。
フローマークが発生するのは、樹脂がキャビティの中を流動する途中の冷却度合いに差があるのが原因です。
成形機のノズル径を大きくする、ノズル温度を上げる、射出スピードを早める、射出圧力を高くする、シリンダー設置点を上げるなどして調整します。
金型の温度を高くする、冷塊だまりをつける、ゲート断面積を大きくする、金型冷却水の位置をゲートから遠ざけるなどしてみることも、冷却度合いの差を少なくすることにつながり、フローマークの発生を防ぐことができるかもしれません。
シルバーストリークの原因と対策
成形品に銀色のすじ状の模様が発生する現象をシルバーストリークと言い、通称シルバーと呼ばれます。
外部に発生した場合見た目にも影響を与え、製品によっては不良品となってしまうことも。
このシルバーストリークは、成形材料の中の空気やガス、水分が表面に現れるのが原因です。
樹脂を溶かすときに発生するガスやスクリューの回転で巻き込まれる空気、射出工程で型に巻き込まれる空気が原因となることが多く、これらの対策が必要になります。
樹脂を溶かすときに出るガスは、シリンダー温度を下げる、ガス排出機能のついたシリンダーの活用、材料の十分な乾燥といった対策が有効です。
スクリューの回転で巻き込まれる空気を減らすためには、射出速度を落とす、背圧を上昇させる方法があります。
射出工程で型に巻き込まれる空気への対策としては、細いランナーやスプルー(スプール)を使う、ガス抜きをするという方法が有効です。
ヒケの原因と対策
ヒケとは、成形品の表面に発生するくぼみのこと。
成形品の厚みに差があるときに生じやすく、解決しにくい現象でもあります。
製品の見た目に影響を及ぼすため、不良品の原因にもなるでしょう。
ヒケも、先に紹介したボイドと同じく、樹脂の収縮率と温度差により発生します。
冷却の際は、樹脂の表面が固まったあとに内部が冷えるという流れになり、冷却した箇所から収縮。
冷却の早い外側に内側の樹脂が引っ張られることにより、表面がくぼむのがヒケです。
収縮分に対する材料の補充圧入が足りない場合は、量を増やすと同時に、保持圧力と金型温度を上げ、スプルー(スプール)とランナー、ゲートを大きくするといいでしょう。
厚みが一定でないと、冷却速度の差で肉厚の場所にヒケが発生する原因になるため、設計段階でできるだけ厚さを均一にしておくのがベストです。
また、収縮率が大きい材料の使用も、ヒケが発生する原因になります。
シリンダー温度を下げ、射出圧力を上げると改善されることもありますが、根本的解決は材料を変えない限り難しいかもしれません。
成形不良も射出成形機の構造に起因するケースがあります。構造について、詳しくはコチラの「射出成形機の構造とスプルー・ランナー・ゲートの特徴」のページをご覧ください。
成形不良品ゼロを目指そう
いかがでしたでしょうか。
この記事で、射出成形における成形不良と対策についてご理解いただけたと思います。
「予見・発見・実現」のプロセスを取り入れたものづくりを提案するジェムス・エンヂニアリングは、成形不良にもしっかりと対応いたします。解析を使って不具合対策もいたします。
解析を使った不具合対策は、射出成形不具合対策も参考にしてください。
射出成形金型を検討しているなら、まず相談してみてください。
またジェムス・エンヂニアリングは韓国HOTSYS社の日本総代理店として、ホットランナーに関して万全のサポートとサービスを提供いたします。
詳しくはコチラのホットランナーシステムのページをご覧ください。