流動解析で見つかる不良を解説。事前対策でコスト削減を実現
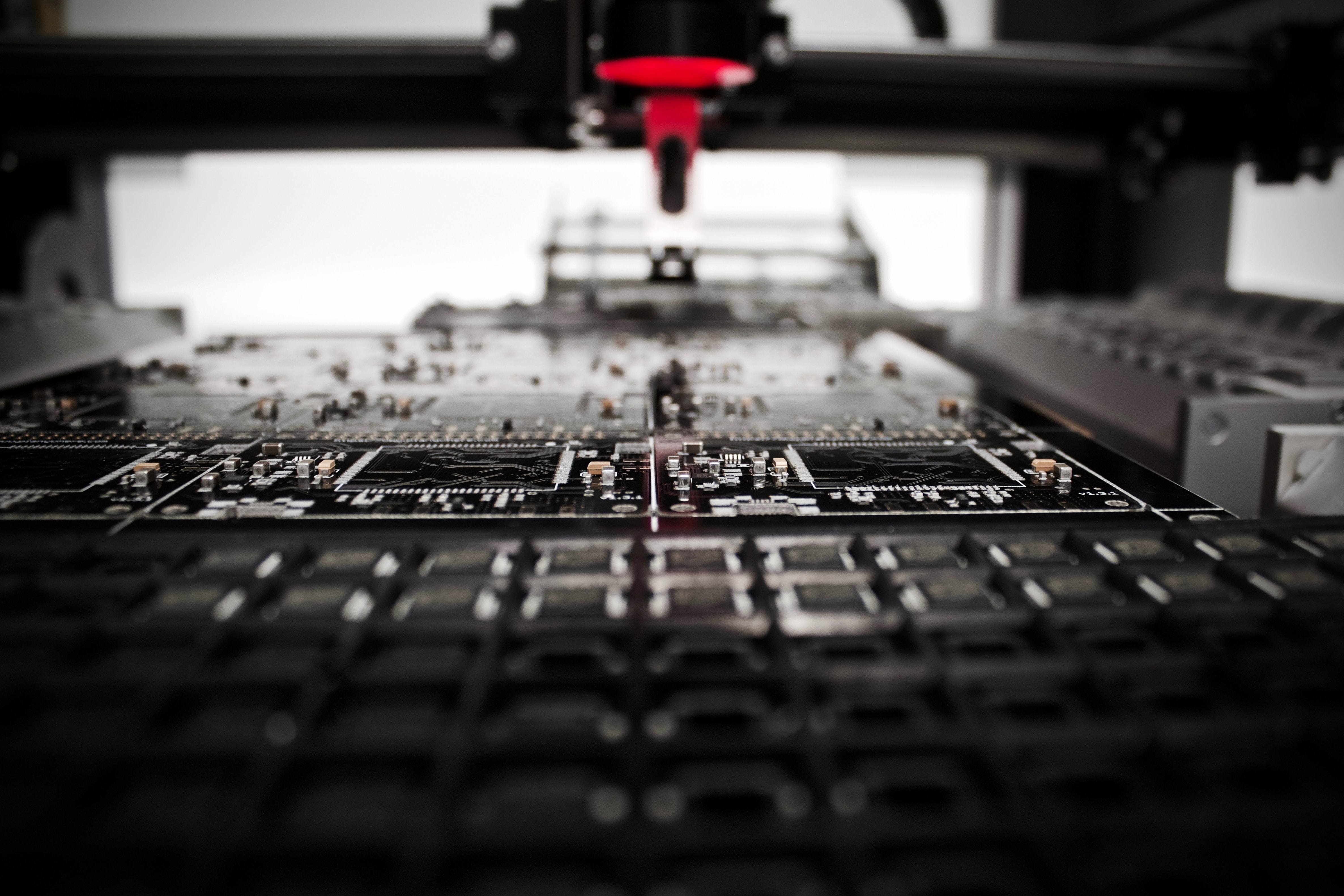
目次
流動解析で分かる不良のひとつ、ためらい現象(ヘジテーション)。
キャビティを充填する樹脂の流れが、薄肉部より厚肉部へ先に充填される傾向にあることが原因で起こる不良のひとつです。
多くの現場では、設計の不備を金型技術者がこれまでに培ったワザでカバーしている場合が多くあります。
図面通りでは樹脂が流れない、速度調整を行いながら何とか充填させているといった声はよく耳にします。
ワザでカバーできない金型は、設計から変更が必要となりコストアップ、納期遅れの原因となってしまいます。
そこで便利なのが流動解析です。
シミュレーション段階で不良を予測し、設計に活かすことでスムーズに樹脂を流せる金型製作できます。
そこで、流動解析で分かる不良について解説していきます。
導入を検討されている方は、ぜひ参考に読んでみてください。
流動解析で見つかる不良
ためらい現象をはじめ、流動解析で分かる不良は多くあります。では、どのような不良を事前に発見できるのか紹介していきます。
ソリ
射出成形時の不均一な収縮や、温度差、配向によって生じるソリ。これは、成形の中で最も致命的な品質不良です。
成形時の圧力分布、温度分布の差、収縮差、温度差により変形が生じます。また、ガラス繊維などの強化繊維では樹脂が流れる方向に繊維が配向する比率が高くなるため、繊維配向による収縮の異方性でもソリは生じます。
よって、流動解析で分析可能なソリが生じる要因は以下3つにまとめられます。
流動解析で分析できるソリが生じる要因
・キャビティ内の温度・圧力・比容積の変化から算出された収縮歪み
・金型温度差
・繊維配向
上記3つのうち、どれが最も影響しているかを分析することが可能です。
また、成形工程ではコントロールが難しい、コーナーやエッジ、肉厚差やリブなどの形状が原因となっていることも解析で分かります。
形状のみに起因するソリの解析もできるので、形状で決まる「ソリの傾向」「ソリやすさ」「どこがどのようにソリやすいか」を簡単、迅速に把握することができるのでとても便利です。
また、成形時の収縮不均一により発生するソリは、どの部位の収縮がどの程度ソリを大きくさせるのかを示す「体積収縮率」の分布で表示されます。
体積収縮率が大きくなる部分ではソリが大きくなりやすく、逆にマイナスに大きくなる部分ではオーバーバック等の不具合が予測されます。
ひけ
成形品の外観不良としてよく問題となるひけ。これは成形品の表面に生じるくぼみを表します。
流動解析では、ひけそうな部位をシミュレーションで事前に予測することが可能です。
ひけを予測する解析方法は2つあります。
ひけを予測する解析方法
・充填保圧解析
・そり変形解析
充填保圧解析では、体積収縮率からひけの予測が可能です。
ひけの量と場所がカラーマップで表示されるのでとても分かりやすいです。
体積収縮率は局所的な体積減少を比率で示した結果で、射出成形時収縮差の影響を考えていきます。
そり変形解析では、離形後に収縮変形からヒケを予測します。
離型後の最終状態を考慮するため、これらの中では一番精度が高いことが特徴です。
ウェルドライン
成形品の表面に現れるウェルドラインも発生しやすい不良のひとつです。ウェルドラインは見た目を左右するだけでなく、強度低下の原因となります。
キャビティ内に流動する樹脂が合流した位置に発生するウェルドラインですが、合流するパターンは2つあります。
ひとつ目は対向流ウェルドです。
穴のある形状で樹脂が穴部を回り込んだあとに合流するときや、異なるゲートから流れる樹脂が正面から合流する場合などに現れます。
ふたつ目は並走流ウェルドといい、同一方向を向いているゲートから流入する樹脂が合流するときなどに現れます。
並走流ウェルドは対向流ウェルドよりは弱めに生じることが特徴です。
流動解析では、ウェルドラインがどこに発生するのかを分かりやすく可視化することができます。
シミュレーションでは、会合角の表示もされるため、ウェルドラインの強弱も把握することが可能です。
ショートショット
成形品の一部が欠けてしまい、不完全な形状になるショートショットも流動解析で予測できます。ショートショットは、キャビティ内に樹脂が完全に充填される前に固まってしまうことで生じます。
小さなリブのある製品では特に発生しやすい不良です。
対策は3つの方法があげられます。
ショートショットを回避する3つの方法
・ゲート位置や、肉厚変更を考慮し、ためらい現象を回避する方法
・樹脂温度・金型温度を変更し流動性を改善し回避する方法
・射出速度を速くし、樹脂が冷えて固まる前に流して防ぐ方法
流動解析でシミュレーションを行うことで、上記3つのうちどれをすればショートショットが回避できるかを予測することができます。
充填解析で流動パターン結果を確認し、上記3つのうちどの対策を行えば回避できるかが分かるので、するべき対策がすぐに分かります。
エアートラップ
エアートラップは、複数のフローフロントが合流するときに気泡が取り込まれて発生します。閉じ込められた空気は、不完全な充填や保圧の原因となり成形する製品の外観不良へと繋がります。
ためらい現象もエアートラップが生じる要因のひとつです。
流動解析では、樹脂の温度、圧力分布、充填パターンを確認しエアートラップの発生位置も予測できます。
ゲート位置の変更や、製品の肉厚分布、材料の変更といった対策方法も提示してくれます。
基本となる流動解析の特徴について抑えておきましょう
このページでは流動解析で見つけることの出来る成形不良について解説してきましたが、そもそもの流動解析の目的などについて知っておくことも大事です。興味のある方は、コチラの「流動解析とは?特徴や注意点を抑えて作業効率の向上を実現」の記事をご覧ください。
流動解析を導入して事前に不良対策をしよう
今回は流動解析で分かる不良について解説してきました。自社にとって流動解析の導入が必要か判断する材料として参考にして頂けましたら幸いです。
また、ジェムス・エンヂニアリングでも流動解析を用いた不良対策を行っています。
流動解析によって不良個所の特定を行いたいという方は、ジェムス・エンヂニアリングの受託解析サービスをご利用ください。